Danny Grimm, of Oregon’s Uplifted is a humble family man and very accomplished, high-grade grower known around the Northwest for his super dank nug and contagious positive vibes. He and his business partner Nate are very hard-working guys and they’ve been at it, for legal reasons we’ll say several years working with some of the world’s top breeders and winning many competitions, even featured in this very magazine for one of their “pheno hunts”. For the last eight years he’s been running a medical grow out of a well-worn 8,000 square-foot building in Salem, Oregon which he has been customizing,
layout and infrastructure, all along the way. With exceptional attention to detail he had every component of his grow streamlined and that’s when the landlord told him about the underground oil storage tanks that had allegedly been discovered underneath his grow facility. The building needed to be demolished immediately and the tanks removed. Worst news ever, right? Or rather an opportunity, as the landlord continued, offering a lease with option to buy on the 52,000 square-foot building right next door, coming available almost immediately.
The building was custom built in 1919, for the Valley Packing Company, a full service beef and pork slaughterhouse and meat packing facility, complete with loading docks. Yes a slaughterhouse! Rad in a creepy way-a cold and vast ominous space-quite large in every sense of the word for two young entrepreneurs working with only their own capital. This was a mega commercial build out, including the entire grid and infrastructure of the four story building but these thirty something’s didn’t even blink at the opportunity. They did a lot of homework and planning, cash flow projections and paperwork, working with the landlord, the local government, utility boards and the state, boot-strapping and generaling this entire build-out themselves. They worked their asses off to make this dream come true, learning a lot of things the hard way along the way. That said, we are grateful for all that they have shared with us, and present to you the roadmap of the nuts and bolts of this mammoth build-out, step by step, in the humble entrepreneurial spirit from which it was born. I’ve witnessed much of this transformation first hand and have been blessed to befriend the kind folks at this righteous family operation as they get comfortable in the new home they have created for the 108 different strains they cultivate. One step at a time they have turned their slaughterhouse into a full-service, state of the art cannabiOne step at a time they have turned their slaughterhouse into a full-service, state of the art cannabis facility from seed and clone to hand-trimmed, top shelf bud and custom extracts. Just as the Valley Meat Co. had the chance to streamline their operation, like a chef would design their kitchen or a craftsman their shop to streamline workflow and maximize productivity, so too would Danny and the team at uplifted have their chance to customize their workspace. So it assumed a natural rhythm a pattern language after consulting…it made most sense with the building construction and cards that were already dealt for the buildings operations, from housing genetics in the form of mother plants, adjacent and easily accessible to the clone room and subsequently veg rooms, flower and trim and extracts. The office is the heartbeat of it all and strategically situated to best manage the trim area where the bulk of the employees are typically lurking. The building was custom built in 1919, for the Valley Meat Packing Co., a full service slaughterhouse and meat packing facility, complete with loading docks. Yes a slaughterhouse! Rad in a creepy way-a cold and vast ominous space-quite large in every sense of the word for two young entrepreneurs working with only their own capital. This was a mega commercial build out, including the entire grid and infrastructure of the four story building but these thirty something’s didn’t even blink at the opportunity. They did a lot of homework and planning, cash flow projections and paperwork-working with the landlord, the local government, utility boards and the state, boot-strapping and generally this entire build-out themselves. They worked their asses off to make this dream come true, learning a lot of things the hard way along the way. That said, we are grateful for all that they have shared with us and present to you the roadmap of the nuts and bolts of this mammoth build-out, step by step, in the humble entrepreneurial spirit from which it was born. I’ve witnessed much of this transformation first hand and have been blessed to befriend the kind folks at this righteous family operation as they get comfortable in the new home they have created for the 108 different strains they cultivate. One step at a time they have
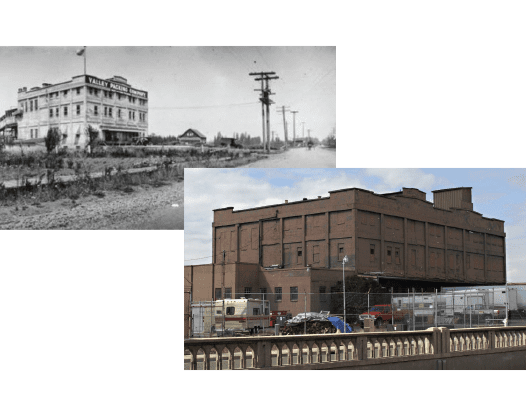
The with the landlord, the local government, utility boards and the state, boot-strapping and generaling this entire build-out themselves. They worked their asses off to make this dream come true, learning a lot of things the hard way along the way. That said, we are grateful for all that they have shared with us and present to you the roadmap of the nuts and bolts of this mammoth build-out, step by step, in the humble entrepreneurial spirit from which it was born. I’ve witnessed much of this transformation first hand and have been blessed to befriend the kind folks at this righteous family operation as they get comfortable in the new home they have created for the 108 different strains they cultivate. One step at a time they haveepreneurial spirit from which it was born. I’ve witnessed much of this transformation first hand and have been blessed to befriend the kind folks at this righteous family operation as they get comfortable in the new home they have created for the 108 different strains they cultivate. One step at his mammoth build-out, step by step, in the humble entrepreneurial spirit from which it was bhis mammoth build-out, step by step, in the humble entrepreneurial spirit from which it was born. I’ve witnessed much of this transformation first hand and have been blessed to befriend the kind folks at this righteous family operation as they get comfortable in the new home they have created for the 108 different strains they cultivate. to be demolished immediately and the tanks removed. Worst news ever, right? Or rather an opportunity, as the landlord continued, offering a lease with option to buy on the 52,000 square-foot building right next door, coming available almost immediately.
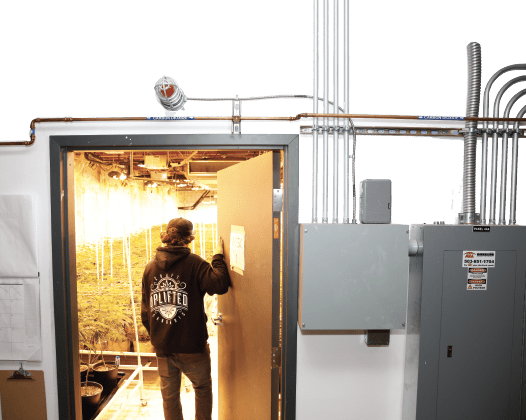
The building was custom built in 1919, for the Valley Meat Packing Co., a full service slaughterhouse and meat packing facility, complete with loading docks. Yes a slaughterhouse! Rad in a creepy way-a cold and vast ominous space-quite large in every sense of the word for two young entrepreneurs working with only their own capital. This was a mega commercial build out, including the entire grid and infrastructure of the four story building but these thirty something’s didn’t even blink at the opportunity. They did a lot of homework and planning, cash flow projections and paperwork- working with the landlord, the local government, utility boards and the state, boot-strapping and generaling this entire build-out themselves. They worked their asses off to make this dream come true, learning a lot of things the hard way along the way. That said, we are grateful for all that they have shared with us and present to you the roadmap of the nuts and bolts of this mammoth build-out, step by step, in the humble entrepreneurial spirit from which it was born. I’ve witnessed much of this transformation first hand and have been blessed to befriend the kind folks at this righteous family operation as they get comfortable in the new home they have created for the 108 different strains they cultivate. One step at a time they have turned their slaughterhouse into a full-service, state of the art cannabiOne step at a time they have turned their slaughterhouse into a full-service, state of the art cannabis facility from seed and clone to hand- trimmed, top shelf bud and custom extracts.
A pattern language The building was custom built in 1919, for the Valley Meat Packing Co., a full service slaughterhouse and meat packing facility, complete with loading docks. Yes a slaughterhouse! Rad in a creepy way-a cold and vast ominous space-quite large in every sense of the word for two young entrepreneurs working with only their own capital. This was a mega commercial build out, including the entire grid and infrastructure of the four story building but these thirty something’s didn’t even blink at the opportunity. They did a lot of homework and planning, cash flow projections and paperwork-working with the landlord, the local government, utility boards and the state, boot- strapping and generaling this entire build-out themselves. They wo asses off to make this dream come true, learning a lot of things the hard way along the way. That said, we are grateful for all that they have shared with us and present to you the roadmap of the nuts and bolts of this mammoth build-out, step by step, in the humble entrepreneurial spirit from which it was born. I’ve witnessed much of this transformation first hand and have been blessed to befriend the kind folks at this righteous family operation as they get comfortable in the new home they have created for the 108 different strains they cultivate. One step at a time they have